How to Pass a 3G SMAW Stick Welding Certification
Passing the AWS D1.1 SMAW 3G & 4G Combo Welding Certification
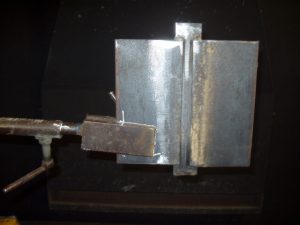
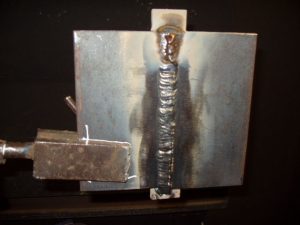
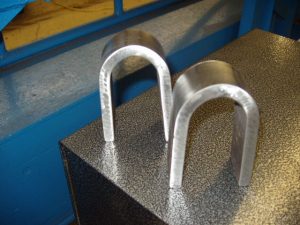
This is about passing the AWS D1.1 3G SMAW welder certification, followed by the AWS D1.1 4G SMAW welding certification. The purpose of this web page is to help anyone out there who is about to take these tests understand the welding procedure, and help give them a visual understanding of this welding certification. As the old saying states, a picture is worth a thousand words!
Why Take the 3G and 4G SMAW Combo Welding Certification?
Since shielded metal arc welding is the process preferred for most outdoor work, it makes sense to have these two welding certifications. The 3 and 4G combo welding certifications, certify you to weld in the 1F, 2F, 3F, 4F positions, and the 1G, 2G, 3G, 4G positions, on structural steel. It also certifies you to do fillet welds on pipe with a minimum diameter of 24 inches.
Originally I was going to take the AWS B2.1 SMAW 6G open root welding certification, but at the moment I am quickly running out of time, and money to take a risk of a harder exam. Plate is very easy to prepare compared to time involved in setting up pipe coupons. The 3G and 4G combo welding certification are the next best thing and are easy to pass. These welding certifications can be used for most industries and should be the bare minimum for anyone who is going to welding school! If you are in welding school don't get tempted to leave school with just a 3G welding certification! Yeah you could get a job with just a 3G welding cert, but going back to school later is not that easy!
AWS D1.1 SMAW Welding Certification Procedure Specifications
The AWS D1.1 SMAW 3G welding certification by itself certifies a welder to weld in the flat, horizontal, and vertical positions, without taking the flat and horizontal welding certifications. When combined with the 4G welding certification this certifies you to weld in the flat, horizontal, vertical, and overhead positions, including pipe that has a minimum diameter of 24 inches.
This welding certification comes in two thicknesses. First the 3/8 inch plate and the second is a 1 inch plate. The test I am taking is the 3/8 inch plate test and it is the limited thickness procedure. It certifies you to weld plate from 1/8 to 3/4 of an inch thick. Personally if I had a choice, I would go with the one inch thick procedure. The 1 inch thick plate is an unlimited thickness procedure, but the school I am certifying at does not offer that procedure.
As with most welding certifications the AWS D1.1 SMAW 3G certification does have an expiration date. This welding certification is valid for 6 months, or 180 days, and if the welder does not weld with this process for six months, it expires worthless. On the back page of the welding certification there is a log table for either an employer or welding school to sign every six months. This provides documented proof that you have been using this welding process you are certified in.
- Welding Process. SMAW
- Vertical Progression. Up
- Joint Type. Butt
- Backing. Yes
- Backing Material. ASTM A36
- Root Opening. 1/4 to 5/16
- Grove Angel. 45 degrees
- Back Gouge. No
- Base Metal. ASTM A36
- Type or Grade. Steel
- Thickness. Groove. (in) .375
- Filler Metals AWS Specification. A5.1
- Filler Metals AWS Classification. E7018
- Electrode Diameter. 1/8
- Amps. 90 to 140
- Electrode Characteristics Current. DCEP
- Shielding Electrode Flux (class). 4
- Stringer or Weave. Either
- Multi-Pass or Single Pass (per side). Multiple
- Interpass Cleaning.Mechanical or Wire Brush
SMAW Welding Machine Set-Up
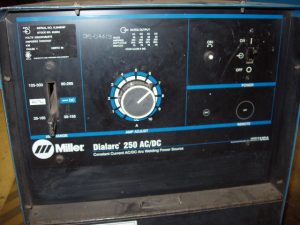
The procedure states that the SMAW welding machine settings for the 1/8 inch E7018 electrode need to be within the range of 90 to 140 amps. The machine I used was a Miller Dialarc 250 set at about 116 amps. This is the amperage I was most comfortable with when I set my machine on a piece of scrap metal welding vertical up. To get this setting I set the amperage range on 35 to 155 range, and then fine tuning the dial to 6 3/4. This amperage is figured out by using the amperage range of 35 to 155. Then taking the higher number, minus the lower number, (155 – 35) and you get 12 amps. The dial setting I am using has a range of 1 to 10; each number on the dial is worth 12 amps. So the starting amperage is 35 amps and then you multiple 12 by the number that the dial is set at. In my case the dial is set at 6 ¾ X 12 = 81 amps, plus the starting range of 35. That equals 116 amps. There is no right or wrong setting for this procedure, as long as you are within the procedure specifications of 90 to 140 amps.
Joint Preparation for the SMAW 3G Welding Certification
The procedure states in the notes how to prepare the test coupons. Here are the AWS D1.1 notes for the 3G SMAW procedure:
1. Grind all hot roll scale adjacent to the bevel, 1" on the front and ¼" back side of the test plate.
2. Grind off all oxidation on the bevel to bare metal. Re-check the bevel angle for the correct angle.
3. Grind all the hot scale off the backing bar to clean metal.
4. The inspector will check the preparation before fitting-up test pieces.
5. After the fit-up is completed the inspector will check all the fit-up specifications.
6. Now the test will be placed in the fixed position. The test piece will be marked in position with a marker and the inspector may see the test anytime during the testing.(DURING THE TEST, THE PIECES SHALL NOT BE MOVED IN ANY DIRECTION AND OR REMOVED FROM THE TESTING PLACE WITHOUT THE INSPECTORS APPROVAL.)
7. The root pace shall be inspected.
8. Required temperatures. ASTM A36, 1/8" to ¾" thick base metal. Minimum preheat and interpass temperatures shall be as follows. When the base temperatures is below 32 degrees, the base metal shall be preheated to a minimum of 70 degrees and the minimum interpass temperature shall be maintained during welding.
Test Coupon Preparation
As the AWS D1.1 3G SMAW procedure memo states I did the following:
This is how the test coupons looked before any grinding or tacking.
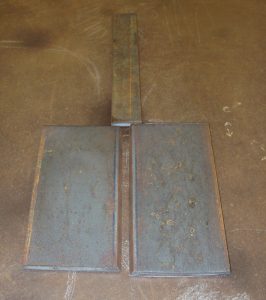
This is a picture of the mill scale ground back a minimum of 1" on the face of the bevel, with the oxidation on the bevel grind-ed to bare metal, and the backing bar grind-ed to bare metal.After that I removed the mill scale a minimum of a 1/4 of an inch off of the back side of the bevels.
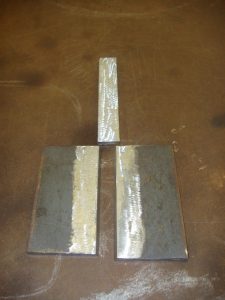
Checking Bevel Angle of Test Coupons
Each right on the mark of 22.5 degrees for a total of 45 degrees. The procedure states the total bevel angle needs to be between 45 degrees and 55 degrees. I am well within the tolerance of the procedure. They are inspected and I get to go to move on.
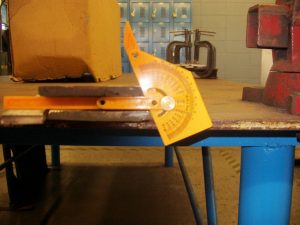
How to Tack Weld Test Coupons
The pictures below are of how I set-up the test plates. First I tacked one side of the bevel to the backing bar. When one side is tacked I used a vice to make sure the bevel is sitting flat on the backing bar. The root opening is set using two 1/8 welding electrodes. I simple put two 1/8 welding electrodes in the root opening, and when I could slide them past each other with just a slight scrape at the tightest point, the root is set to the proper width.Once I set the root opening and have one side tacked, I use a vice to clamp down the bevels to the backing bar and tack it into place. Finally I tacked the middle of the plate to the backing bar using the vice again. This is done to keep the backing bar flat against the bevel.
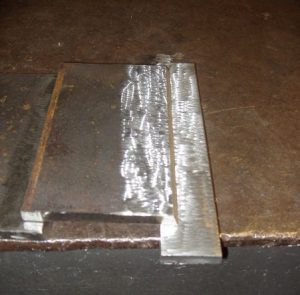
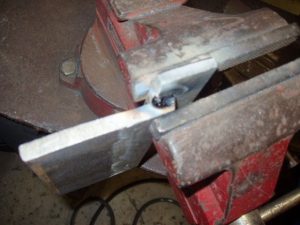
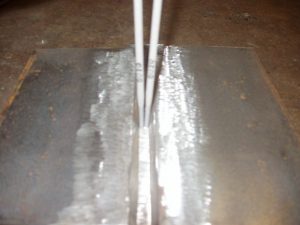
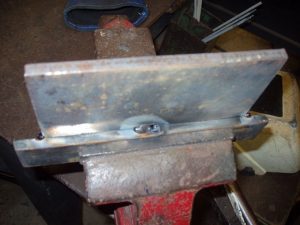
Pre-Inspection of the Beveled Test Plate
The plates are put into position and inspected. The arm holding the plates is marked in many places to ensure I do not move the test coupon when welding or cleaning.
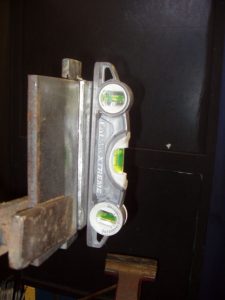
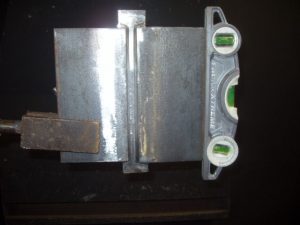
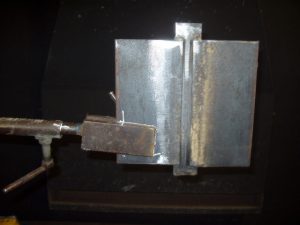
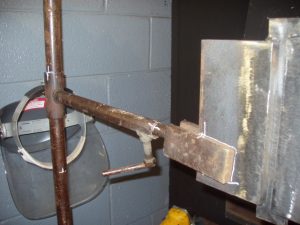
Techniques for Passing the AWS D1.1 SMAW 3G Welding Certification Root Pass
How to Do a Vertical Up Root Pass in the 3G Position with a Backing Bar
Starting the root weld did not require a preheat as the temperature was about 70 degrees outside. To start the root I got comfortable and started to weld. The technique I used was a side to side weave. I hold the sides of the bevel where the bevels edge feathers into the backing bar until I could see the arc of the electrode start to roll to that side. Once the arc is rolled and the flux is burned off on that side of the electrode, I weave onto the other side, and keep repeating that process. By allowing the arc to roll on the electrode it penetrates the bevel and gives the electrode a chance to ride up on the bevel for a moment. This helps to avoid slag inclusions. I used three welding electrodes and had two restarts.
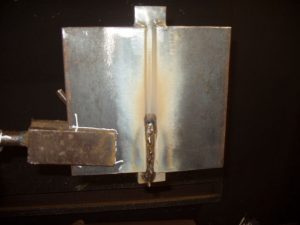
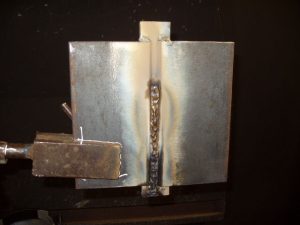
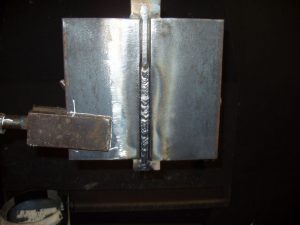
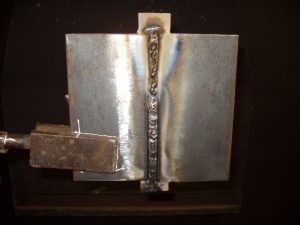
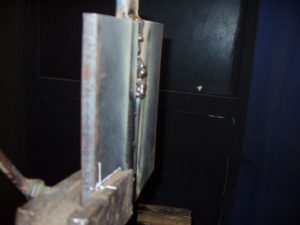
The root weld was cleaned with a wire wheel and as the procedure states it was inspected. This is done because it is in the welding procedure and in the words of the American Welding Society:
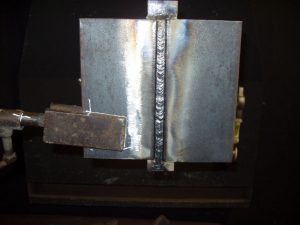
"The root of the weld shall be inspected, and there shall be no evidence of cracks, incomplete fusion, or inadequate joint penetration. A concave root surface is permitted within the limits shown below, providing the total weld thickness is equal to or greater than that of the base metal. The maximum root surface concavity shall be 1/16 in. (1.6 mm) and a maximum melt-through shall be 1/8 in. (3 mm)"
Before moving onto the hot pass or filler pass, I let the plate cool till I could almost touch it with my hand. Second I did take a grinder and lightly ground the root pass. I did not need to do this, but why take a chance! Here is the root weld ground down.
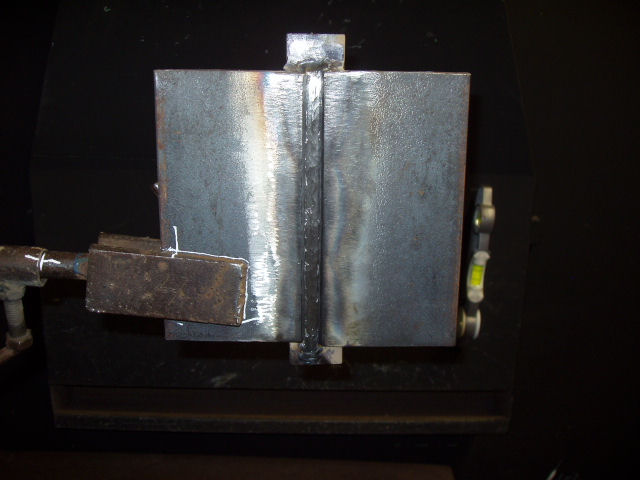
3G Test Fill Pass Welding Technique
For the hot pass or fill pass I used the same technique as the root weld. That is holding the sides and rolling the arc until the weld rides up onto the side of the bevel. I used four electrodes and had three restarts.
Again I waited for the plate to cool and lightly grinded it down. I did not have to grind it, but why risk getting a slag inclusion. As you can see the first restart was a little rough.
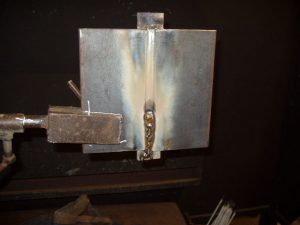
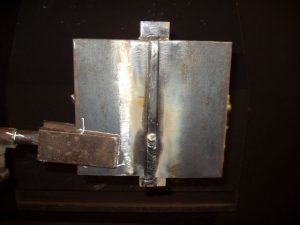
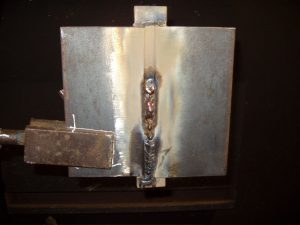
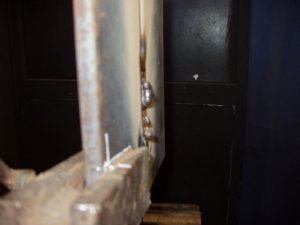
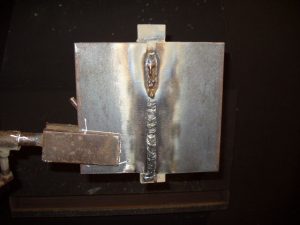
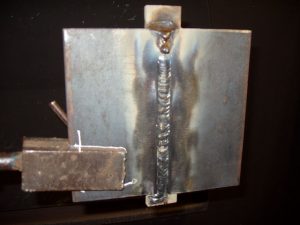
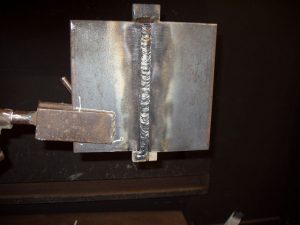
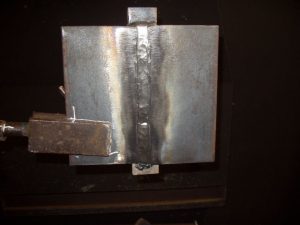
Weave Techniques for Vertical Up Cap Cover Pass Weld
The cap was done using a weave technique holding the corner of the bevel until it was filled and the moving onto the other side. If you do not wash weld properly into the corner of the bevel you run the chance of not penetrating the test coupon properly. On the cap of the weld I used four electrodes. Here are the picture of the cap weld.
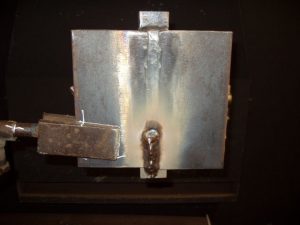
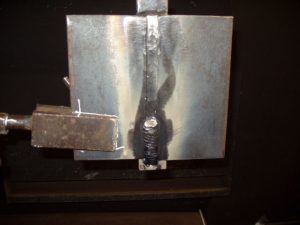
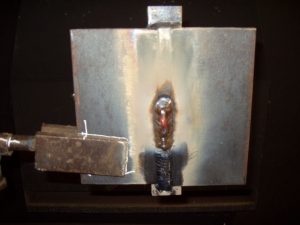
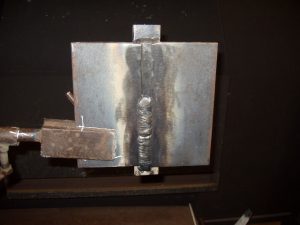
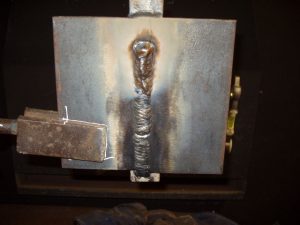
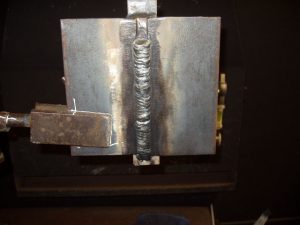
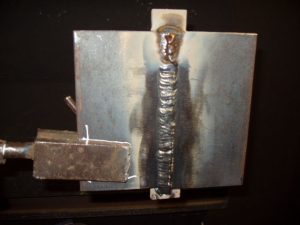
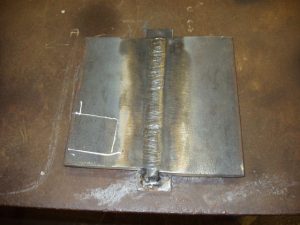
Welding Techniques for Welding a Weave Vertical Up Weld
Here is where I held the electrodes when weaving the cap of the weld. As you can see the center of the electrode needs to be directly on the corner of the bevel. This gives the cap good penetration into the test coupon and keeps the risk of a face bend break to a minimum.
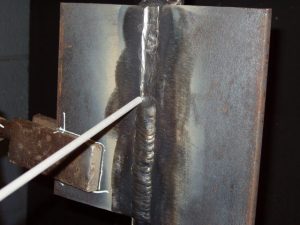
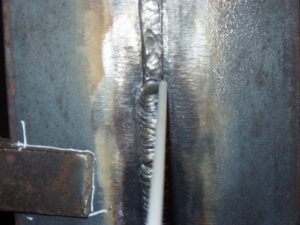
Finished 3G SMAW Welding Test Ready to Inspect

This is the finished weld and cleaned with a wire wheel. It is well within the acceptance criteria. In the words of the American Welding Society:
"The face of the weld shall be flush with the surface of the base metal, and the weld shall merge smoothly with the base metal. Undercut shall not exceed 1/32 in. (1 mm). Weld reinforcement shall not exceed 1/8 in. (3 mm)"
How to Prepare Test Coupon for the Destructive Bend Test
Preparing test coupons for a bend test is not difficult but it does require taking your time and doing it right. There are a few steps that need to be followed otherwise you may fail this test based on preparation!
Weld Test Coupon Marking and Cutting
It is now the next day since taking the test and the plate has had more than enough time to cool.
The first thing is to put a mark in the center of the plate with soap stone. Then you need to put a mark one inch above it and one inch below it. Then the next marks are 1½ inches above the top mark and again 1½ inches below the bottom mark. The two outside marks are the bend specimens. Using a square I marked lines across the test plate as to where they will be cut. In the case of coupon failure the middle of the plate can be used as a backup coupon, as long as the failure of the bend falls within the AWS acceptance criteria for a bend test.
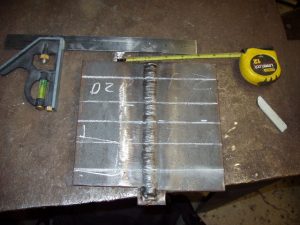
Next my initials are inscribed, and the bend test specimens are marked, one for a root bend, the second for a face bend, and the third for an alternate. Just as a not the bend test specimens must be a minimum of 1 1/2 inches wide.
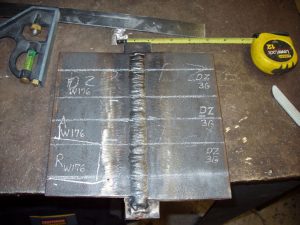
Cutting Test Coupons
The test coupons are cut on a band saw.
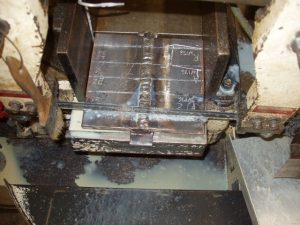
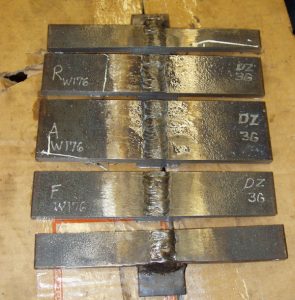
How to Remove a Backing Bar from Structural Welding Certification
Now it is time to remove the backing bar off the test specimens. I did this by grinding the area where the root penetrates the backing bar. I grind just close enough to where I could lock on to the split backing bar with a vice. Then I put the backing bar into the vice with one side of the backing bar locked and pushed down with my hand on the coupon like a lever.
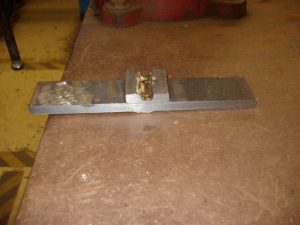
The backing bar came off very easily. In my previous welding certification I used a chisel to remove the backing bar. Unfortunately with a chisel you run the risk of gouging into the test specimen. I personally think using the vice was a lot easier then using a chisel. I repeated this until the entire backing bar was removed.
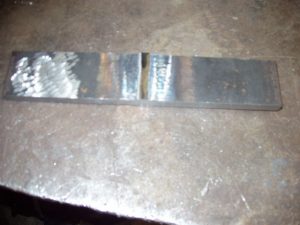
Weld Reinforcement Removal
Before grinding down the root and cap of the weld I took a center punch and marked the center of the weld. This is done to make sure the weld area is what is being bent. Next I grinded down the root and face of the weld until they were the thickness of the test plate. Followed by sanding the corners, and a light brushing with a buffing wheel, this was done to see if there was anything hiding under the surface. As a note if you grind below the surface of the test coupon the test will automatically be rejected!
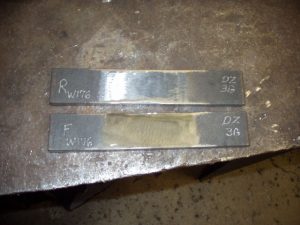
Before grinding down the root and cap of the weld I took a center punch and marked the center of the weld. This is done to make sure the weld area is what is being bent. Next I grinded down the root and face of the weld until they were the thickness of the test plate. Followed by sanding the corners, and a light brushing with a buffing wheel, this was done to see if there was anything hiding under the surface. As a note if you grind below the surface of the test coupon the test will automatically be rejected!
Welding Certification Bend Test
I will have two bends done. The first will be a face bend and the second will be a root bend. In the case of a failed bend test, I can still use the center of the plate as a backup coupon, as long as it falls within the acceptance criteria.
Here are the acceptance criteria for the bend test in the words of the American Welding Society:
"Acceptance Criteria for Bend Tests. The convex surface of the bend test specimen shall be visually examined for surface discontinuities. For acceptance, the surface shall contain no discontinuities exceeding the following dimensions:
(1) 1/8 in. (3 mm) measured in any direction of the surface
(2) 3/8 in. (10 mm) – the sum of the greatest dimensions of all discontinuities exceeding 1/32 in. (1 mm) , but less than or equal to 1/8 in (3 mm).
(3) ¼ in. (6 mm) – the maximum corner crack resulting from visible slag inclusions or other fusion type discontinuities, then 1/8 in. (3 mm) maximum shall apply
Specimens with corner cracks exceeding ¼ in. (6 mm) with no evidence of slag inclusions or other fusion type discontinuities shall be disregarded, and a replacement test specimen from the original weldment shall be tested."
Root Bend Test
Here is the specimen for the root bend, followed by the bending, and finally successfully passing the root bend test.
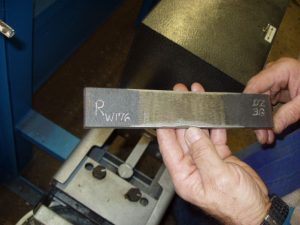
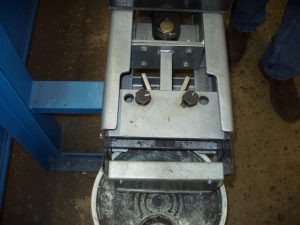
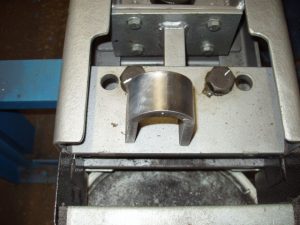
Face Bend Test
Here is the specimen for the face bend, followed by the bending, and finally successfully passing the face bend test.
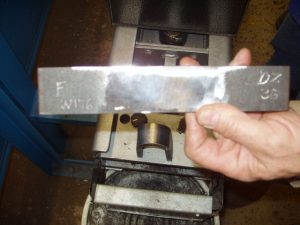
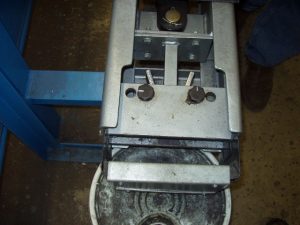
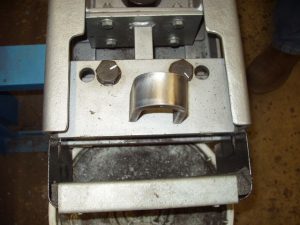
Now I am ready to take Stick/SMAW 4G Welder Certification in combination with this one to be certified to weld in all position and that includes fillet welds on pipe over 22 inches in diameter.