MIG Welding Stainless Steel
How to MIG Weld Stainless Steel and Nickel Based Alloy
MIG Welding Stainless Steel and Nickel Based Alloys is pretty straight forward. The weld has many of the same characteristics as a carbon steel weld. In reality you should not be welding stainless steel or nickel based alloys until you master carbon steel. Besides a easy learning curve the MIG Welding Process works on stainless steel just fine with the exception of two issues:
- Joint Set-Up/Weld Joint Distortion
- MIG Gun Cord/Liners Issues
How to Setup and Control Distortion On Stainless Steel Welds
Joint set-up for stainless steel requires a pretty cleans surface but the real big issue controlling metal distortion. Obviously a clean joint is ideal for all welding situations so the same rules apply to stainless steel as carbon steel. The distortion of the weld is controlled in two ways:
- Bracing the Weld Joint
- Spreading Out the Heat
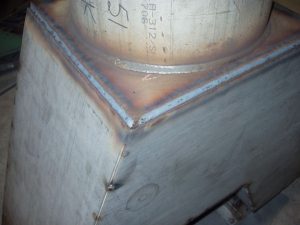
How to Brace and Control Weld Distortion?
Bracing the Weld joint is done in many ways. It can be as simple as wedging a piece of wood between two sides to keep them from closing in (hopefully you will be able to remove it later). All the way to creating a scaffold like system of supports put in place to control the distortion. Each weld joint is different in terms of "How do I brace it to control the distortion". Another way of bracing the weld area is building a jig to keep all of your parts in place while welding. It really comes down to each situation is different and how much weld is needed. The more welds that are needed the more bracing you will need. With stainless steel and nickel based alloys every joint needs bracing and that also includes spot and tack welds. Stainless distorts just that much.
The Big lesson for MIG Welding Stainless Steel is brace your joints well, make as many tack welds as needed and spread your heat evenly throughout the joint.
Spreading Out the Heat
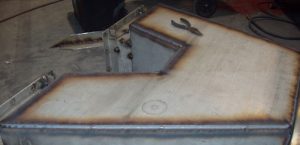
Spreading out the heat is the main technique for welding g Nickel Alloys and Stainless steels. The weld is spread out by staggering, back stepping and/or waiting for the joint to cool before welding any further. Stainless heats up very quickly and holds that heat for a very long time compared to MIG welding carbon steel. The distortion heat causes can literally be seen as you weld. Thin Stainless Steel will move inches as you tack weld and a simple 90 degree tee joint can distort as much as 45 degrees.
Most Common Electrodes and Gas for MIG Welding Stainless Steel
The most common electrode to weld stainless steel is the ER308 L and the gas type is C2 or 2% Carbon Dioxide and 89% Argon.
MIG welder setting for stainless and most nickel based alloys are very similar. You can ask your welding supplier for recommendations or if you have a MIG welder that has a electrode wire and gas selection chart inside like in the picture below you can follow that. If you want more detailed information on stainless steel electrode and gas choices and options click here.https://gowelding.org/welding/mig-gmaw/stainless-steel-electrodes-and-gasses/
