MIG Welding Techniques
Is MIG Welding Easy?
Yes MIG welding is very easy if you take the proper steps to set up your machine, choose the right settings and use the right technique.

How can I improve my welding skills?
Here is the inside scoop about MIG welding techniques and skills. They are not much different than any other welding process. It comes down to a few basic fundamental rules that are the core of any welder's skill level. The following tricks and tips are what separate professional first class MIG welders from the rest:
- Set Your Machine Right
- Have a Clean Joint
- Use the Right Technique
- Comfort is the Golden Rule
Knowing How to Set Up a MIG Welder
When it comes to MIG welding a properly set up machine is the most important part. MIG welding is easy but machine set-up it critical and requires a strong knowledge of the proper settings. Other processes like Stick and TIG you can get away with a machine that is not set exactly right. When using a MIG welder there is no room for error! Don't get comfortable using just one machine when learning!

The Importance of Joint Preparation
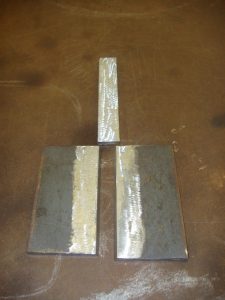
Joint set-up is always important and even if you are the world's best welder then you will always have a clean joint. I personally know two welders that won the world's best welder title and both of them rely heavily on having a clean joint. They are not special in any way except for the fact they know how to follow a procedure properly. The bottom line is there is nothing that you can do to fix a weld if the joint is dirty. If you put junk into the joint then you get junk out of the weld. Got it!
What Welding Technique to Use?
Always use the right technique for the type of weld you are doing. Not every technique is right for everyone and not technique works on every joint in any position. Nothing works all of the time and it comes down to what works right for you. Weld techniques are the smallest factor in MIG welding! Further down on this page there will be information on different welding patterns to use.
The Best Welding Technique to Use?
Finally the GOLDEN RULE of MIG welding Techniques! If you want a sound quality weld that looks good you need to be comfortable and take you sweet time. Using anything you can find to get comfortable is what separates first class welding technicians from the rest of the pack! You need to lean on something to keep your body and hands steady! No welder that does critical weld joints ever welds unless they are comfortable. A common trick Foreman use to get welders to fail or bust out on the tests is rushing them through the test to see what they are made of!
Every welders hands shake and all of our bodies will move when we breath, sneeze or the floor moves. Get intimate with the weld joint and make it feel like home. I have been in some tight spaces that looked impossible but once you get in there you find sweet spots that will bring comfort and control once you give it enough time to become home. That is what separates the best from the rest!

Take a closer look at the picture below. The welder in this picture has been welding for 20 plus years and really knows what he is doing. He is using the steel plate on his back side to lean on, then he is kneeling for even more stability and on top of that he is bracing his hands. That is how you get comfortable. I do want to point out that this picture was taken on a ship that was sailing in rough seas and everything was moving. He is so well braced into his weld area that even if the ship came to a sudden stop he would barely move.

Should I MIG Weld Forehand .vs. Back-Hand Welding?
There are two ways to MIG weld. The first and the most common is to push the MIG gun toward the direction of the weld, this is called forehand method. Forehand welding produces shallow penetration with a flat wide smooth surface. The second is backhand method where you drag the MIG gun like a Stick welder. This produces a deep penetration weld that is narrow and is high in the center. In most cases you will be forehand welding and it is very rare to do backhand welding.
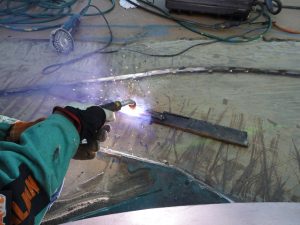
How Much Should a MIG Welder Wire Stick Out?
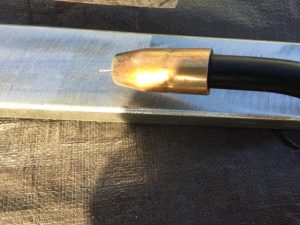
Electrode or the wire stick out should be about 3/4 of an inch. Less is OK but a much longer wire stick out won't allow the shielding gas to do its job properly. I do want to mention that the shielding gas flow rate needs to be right for the stick-out. Too much gas causes turbulence even if the stick-out is just right and too little gas does not provide enough shielding gas. It is a balancing game that requires judgment for the situation. Just keep your stick-out between ¾ of an inch at the max to ¼ of an inch at the bare minimum.
MIG Welding Pattern
Patterns for MIG welding are most likely what you are here for! Guess what? A properly set-up machine, clean weld joint and a comfortable position have more to do with a quality weld then technique! What patterns do is compensate for a lack of skill. Most welders that have been around adapt in a second to the joint and just know how to weld. This all comes in time so patterns are kind of a crutch until you learn to go with the flow (literally metal flow). What patterns do is help spread out the weld the way you would spread peanut butter on bread. It makes thing smooth and uniform. The four most common patterns are:
- A Steady Motion
- Whipping
- Circles
- Weaves
Steady Motion Welding Technique Pattern
A steady motion is the most basic technique and requires the MIG welder be set exactly as needed. It is what most robots use to weld and it can produce a perfect weld in any position. It comes down to machine settings, electrode angle and travel speed. The basics of a steady motion are the hotter the setting in most cases the better the weld. There is not much to this technique except get everything set right. I do want to mention this is the techniques used for most out of position aluminum MIG welding. Besides that it is all self explanatory.
Whipping Welding Technique Pattern
Whipping works well on most joints using either stringer beads or fillet welds. It keeps the puddle in a tight range but also preheats the joint prior to filling it with metal. This technique is great for beginner welders to learn how to control their travel speed. It is a simple pattern that requires two steps forward and one step back. It is real simple like walking by putting one foot in front the other.
Circle Welding Technique Pattern
Circles are the happy medium between whipping and weaving. They work well on most joints and can be applied almost anywhere. The way it works is make a small circle and then go forward and do it again.
Weaving Welding Technique Pattern
Weaves are used for wider welds and range from a tight side to side motion that can be a stringer bead to welds that are wide and big for a single pass. Weaves are good for big joints that have no distortion issues. Just as a note in most shipyards weaving is not allowed. There is a formula that allows so much heat at a certain travel speed that excludes weaves from critical joints.
Welding Positions and Techniques
Some general guidelines for MIG welding techniques are as follows and they are only guidelines:
Flat Position MIG Welding Techniques
Flat welding is the easiest. Typically the MIG gun will be pushed, the angle of the MIG gun can be pointing straight down to leaning toward the direction of the weld up to 35 degrees. Use a high voltage setting that runs fast and hot. A steady motion works well here but any pattern will too as long as the weld penetrates. If you are new to this then crank up the machine as high as you can. It is good practice and insures the weld will penetrates.
Horizontal Position MIG Welding Techniques
Horizontal welding is a little harder. The MIG gun should be pointing upward between 35 to 45 degrees and tilting about 15 to 35 degrees toward the direction of the weld. You need to watch out for overlap and the weld rolling over. Always keep it to a tight stringer beads on any joint. Whipping and circles work best here. You can't crank up the machine setting to compensate for a lack of skill. The weld needs to be spread out and controlled with skill and technique.
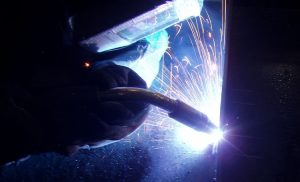
Vertical Down MIG Welding Techniques
Vertical down is also pretty easy. You start on the top and work your way down. The MIG gun needs to be tilted up between 35 to 45 degrees. There is a trick to welding vertical down. You need to stay ahead of the puddle and keep the electrode moving from side to side. Otherwise the weld will not penetrate properly. Patterns don't really count as long as you stay ahead of the puddle.
Vertical Up MIG Welding Techniques
Vertical up is the most difficult of the MIG welding positions. The MIG gun handle should be pointed up between 35 to 45 degrees. When welding vertical up you need to build a shelf of weld to work upward on. The vertical up weld in MIG is typically very convex. Quick hint; if you need help with welding vertical up it always a good idea to grind a small grove where you will be welding. This is one of those positions that really sucks and no matter what you do the weld will never look just right. If the weld is wide enough then you will get a decent looking weld but otherwise it is a very convex weld in appearance.

Overhead MIG Welding Techniques
Overhead MIG welding requires the MIG gun tilted 5 to 35 degrees toward the direction of the weld. You want the heat to be on the hot side and once you do it for a while it is as easy as flat! There will likely be a bit of spatter falling (a lot if it is heavy plate) so you need to control those sparks enough to keep them away from you. The biggest safety concern is make sure your sleeves are tucked in. Otherwise you will get a bunch of molten metal in your sleeve that is going to burn up you elbow.
Overview of Welding Techniques
The general guidelines for MIG welding are whip when welding thin metal or making the first pass in a joint, circles for a both thicker materials and wider welds. Weave for vertical up and down. My personal preference is to have the voltage at the maximum recommendation and just hold the MIG gun steady letting the MIG welder do the work. If you are MIG welding in a shop chances are all of the welds will be done in position.
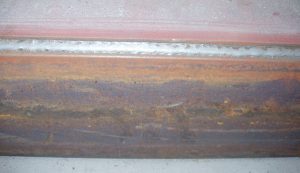
In a past employer's shop, I welded 1/2 in. plate; I always used a minimum of 32 volts to weld with. The type of transfer is changed with the wire speed. If I wanted to spray I would just turn down the wire speed and then it would spray. If globular transfer is needed I increased the wire speed a little. Finally if short circuit is needed I crank the wire speed to a much higher level. The picture on the left is a horizontal filet weld I did on 1/2 plates to 12″ channel using spray transfer at 36 volts, .035 wire, and the wire speed approaching 900 inches per minute (very hot). The welds are about 5 feet between restarts and the machine was running so hot that if I were to pause for too long it would blow a hole through the metal. MIG welding is excellent for production!