TIG Welding Pipe
How to Walk the Cup?
Walking the cup is a welding technique that is almost exclusive to TIG welding pipe! This technique is the industry standard for TIG welding pipe. Many companies that hire TIG welders won't even consider someone if they do not weld pipe by using the walking the cup technique. My personal experience is that every interview I had for TIG welding pipe was about do I know how to walk the cup.
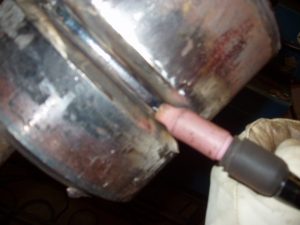
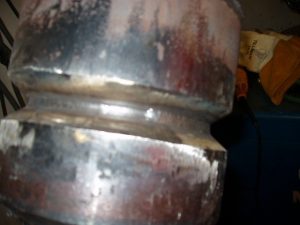
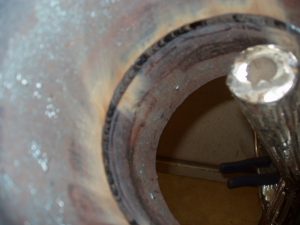
There are three ways to walk the cup:
- Ratcheting the Cup
- Wobbling the Cup
- Sliding the Cup
How to Ratchet the Cup?
The first is the ratchet technique it is just like turning a ratchet on a bolt. Ratcheting the cup is typically used anywhere there is a flat area to lean the TIG torch cup on. This is done by placing the cup on the pipe and turning the handle just like a ratchet on a bolt. The forward motion is created by having a slight twitch of the wrist at the end of each ratchet reversal. This is the hardest technique for walking the cup but also the best when it comes to weld quality. The reason behind this is the arc length is kept extremely close to the puddle while maintaining a consistent height at all times.
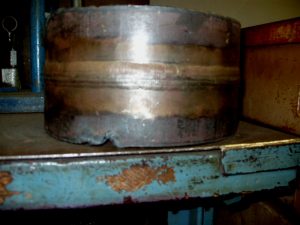
How to Wobble the Cup?
The second way to walk the cup is to wobble the cup side to side like moving a heavy barrel that is standing. This is typically used with a larger cup sizes and is best used on a flat surface or directly over another weld. This method is a lot easier the ratcheting the cup but also not as precise! This is because the arc length is always changing from the wobble of the cup. It still beats free hand welding and I use still use it in tight spots where I need to weld left handed with a mirror. Wobbling the cup is a good start to learning to walk the cup. Once wobbling the cup is mastered it's time to take it to the next level by mastering ratcheting the cup. This is where you will learn to perfect TIG welding pipe.
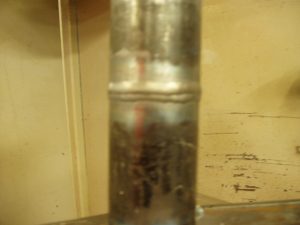
How to Slide the Cup?
Sliding the cup is just that! The cup slides and you literally push it to guide the tungsten to where it needs to be. Sliding the cup is done anywhere that is too odd of a surface to walk the cup. More commonly sliding the cup is used in the grove of a heavy wall pipe. You have a large bevel with a cup size that fits between the joint. Simply set your tungsten to the right height and start sliding the cup from side to side and forward to spread your filler wire. Sliding the cup is also used for putting in the root and hot pass on a heavy wall pipe.
This technique is never mentioned in welding books but is typically learned in the field. Sliding the cup is also used when a pipe is almost filled and ready for the cap. In this case, the surface the cup is leaning on is not flat enough to walk the cup and not deep enough in the grove to slide the cup. Compromise is what is needed! You do whatever it takes to fill the joint. Most of the time half the motion of the cup is sliding and the other half is walking it. It's a little tricky but just takes some time to get used to.
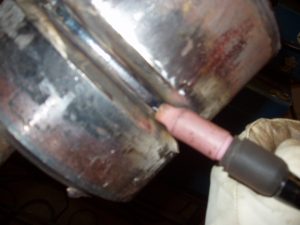
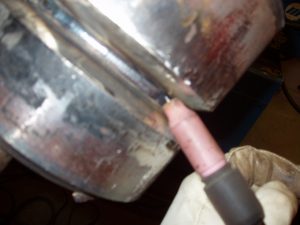
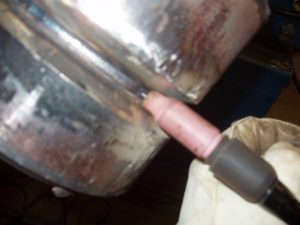
TIG Welding Pipe with an Open Root
When it comes to TIG welding pipe with an open root the joint preparation is more than half the battle! The bevel must be Clean and Even all the way around the pipe. The mill scale should be ground back at least 1 inch on the inside and outside of the pipe. The bevel should have a feathered edge and the gap should range between 1/16" to 1/8 of an inch depending on the size of the filler wire being used. For most students practicing in school the gap can be set by using a TIG wire bent into a V. Simple place the TIG wire on the bevel and then place the other coupon on top of it. Make sure the pipes are aligned properly. The main thing is you want the gap to be even all the way around the pipe and just small enough to put your filler wire into the groove without it being able to slip inside the pipe.
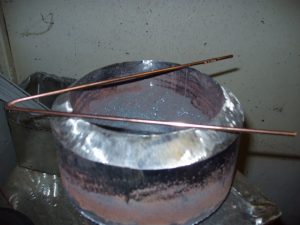
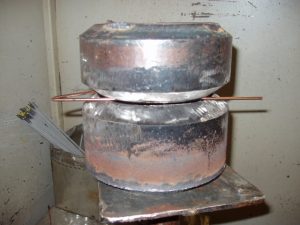
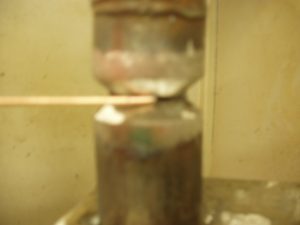
Tacking the Pipe
Tacking the pipe is done by placing the filler wire into the grove and going over it with the TIG torch. If you will be using a 1/8 filler wire you will set the gap with a 1/8 filler wire. To tack the pipe you want to find a spot that the filler wire can't slip through the grove. Then simply tack the pipe. Once the first tack is in you need to puller the spacer out a little very quickly. What will happen is the tack will shrink and then you put in another tack on the opposite side of the pipe. Once the first two tacks are in you will need to pull the spacer out. Now check the gap all the way around the pipe and make sure it is even. If not make some adjustments. Ideally you want the tacks to be about ¾ of an inch long.
The technique used to tack the pipe is almost a shake of the TIG torch. You place the filler wire into the groove and run over it while making sure you fuse both sides of the bevel. When you get to the end of the tack stop your arc and do not pull out your filler wire! Wait a second for the tack to cool and then break off the filler wire from the tack. This is done to avoid creating a keyhole that would later create a lump in the root when you try to tie in the root into the tack. Once all of the tacks are in you should feather the tacks before putting in the root. If the tacks are not perfect don't worry because you will go over them when you put in the root. When you go over them on the root pass they will smooth out and be barely noticeable. After each tack make sure you cut off the end of you filler wire to get rid of any contamination.
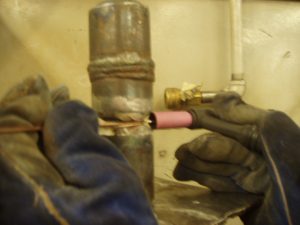
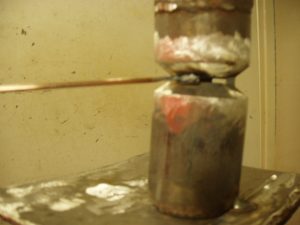
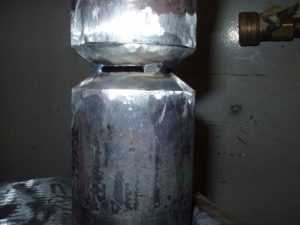
After each tack make sure you cut off the end of you filler wire to get rid of any contamination. A contaminated filler rod will cause problems with the weld and at the same time make the tack or weld difficult to do. When it comes to TIG welding the trick is to have everything clean. That means the joint, filler wire and the tungsten must all be extremely clean. The picture of the tungsten electrode below is a perfect example of a contaminated electrode that needs reshaping!
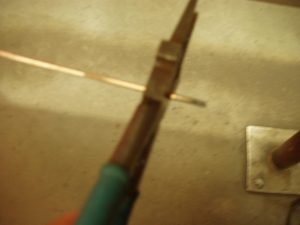
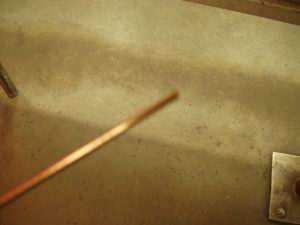
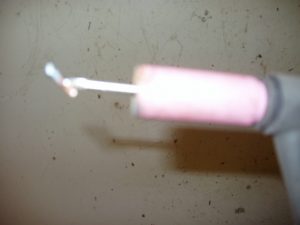
Pipe Welding Techniques for an Open Root
When it comes to the techniques used for TIG welding an open root there are two ways to do it. It comes down to where you learned to weld. In America the southern states weld different then the northern states. The northern states just lay the filler rod in the bevel and walk over it. That's me the Yankee! In the southern states, mostly on the Gulf of Mexico, they use a smaller diameter wire then the root opening. What they do is feed the wire from the opposite side of the pipe by leaning it on a tack. The filler wire is literally being feed from the inside of the pipe! It's not easy but knowing how to do that is really good if your pipe has a bad fit-up. Personally just running over the wire works for me and is a lot easier then feeding the filler rod!
The welding technique used will depend on the thickness of the pipe. On thin wall pipe you can either ratchet or wobble the cup. This is because you will have a shallow bevel that you can walk on with the cup. If it is heavy wall pipe you will want a cup size that is small enough to fit between the groves and slide easily.
Before starting to weld you need to cut your filler wire on an angle to match the feathered tacks. Then place the wire on the feathered tack and strike an arc in the middle of the tack. Wait for the tack to start melting and slowly walk the cup toward the filler rod. When you get close to the filler wire you will want to keep the wire pressed into the root and slowly approach it. Move slowly enough that the filler wire becomes fluid and sucks itself into the tack. At this point the travel speed is picked up and you keep walking the cup. When walking the cup do not wash the root too far onto the sides of the bevel. If you do you will get suck back or a concave root surface. Once the weld is ready to tie into the next tack, start to slow your travel speed down. Approach the tack slowly while pressing the filler rod into the tack. Once the filler wire reaches the tack start to press and lift the filler wire to at least a 45 degrees or more when tying into the tack. If you do not lift the filler wire and create a steep angle you will likely create a hole before the tack is tied in properly. Breaking the arc off of the tack needs to be done by quickly increasing your travel speed and long arcing off. This is done to prevent a fish-eye. The finished root pass should be smooth all around. The tie-ins should be barely noticeable and the root surface should be flat to convex. A flat root surface is not a big deal because it will push in more on the hot pass.
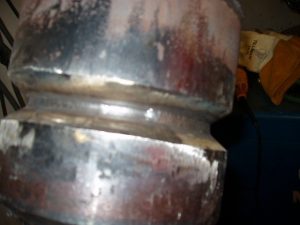
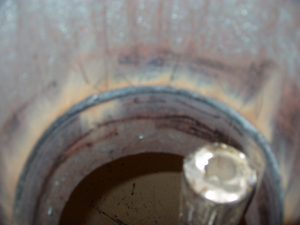
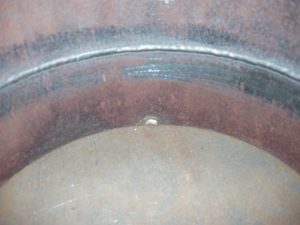
Common Problems with Open Root TIG Welds
When it comes to open root TIG welds there are some common problems but all of them are easy to fix. TIG welding is a very forgiving process! Here are some common problems with open root welds and there solutions:
Concave Root Surface or Suck Back
- Increase your travel speed
- Lower the amperage
- Don't wash to far onto the bevel
- Increase the TIG torch angle
- Filler wire is to large
- Shielding gas flow is to low
- Increase the angle of the filler wire
Pipe Welding Techniques for the Hot Pass and Filler Passes
When it comes to the hot pass and filler passes they are just like to root pass but require a higher heat setting. For example if you are welding a 2" schedule 160 pipe the root pass will require about 90 amps and the hot pass will require 125 amps. On heavy wall pipe the technique used is sliding the cup. On thin wall pipe the technique used is walking the cup. This is because the bevel is shallow enough to allow the cup to walk on the edges of the bevel.
The general rule for these passes is keeping them under 3/4 of an inch wide. After that, start doing multiple passes. The hot pass is also where you will be able to push the root pass in to fix a flat or concave root surface. On the hot and filler passes you want to wash into the bevel very well. Unlike the root pass where you a focusing on pushing the filler wire into to grove here the main focus is on washing the filler wire onto the sides of the bevel. The fill pass does get tricky if you are almost done filling a heavy wall pipe. This is an area that will require compromise when it comes to the welding technique used. It typically takes half the motion of sliding the cup and the other half walking the cup.
When selecting a cup size for heavy wall pipe it is very common to use multiple cups depending on the thickness of the grove. Most times you start with a smaller cup and work your way up to larger cup sizes depending on how much if the grove is filled. The idea is to use a large enough cup that will slide in the grove above the weld without touching the weld. Once the pipe is almost filled up you go back to a smaller cup so that you can build a shelf of weld and start the transition to walking the cup.
Pipe Welding Techniques for the Cap
Welding the cap on a pipe is no different than walking the cup on any other surface. Ideally you want to ratchet the cup but if you are not there yet just wobble the cup. The cap weld does have some common problems that are easily solved. The most common problem with the cap is undercut. Undercut is typically solved by cleaning the weld area before each pass with a sanding disk or file. What happens is each pass that you weld creates a heat affected zone. What needs to be cleaned is the surface of the pipe that is going to be welded. This area typically has a blue tint to it that shows you the heat affected area. Just remove the surface metal with a file or fine sanding disk! This applies to all restarts and stringer beads. After that the weld should flow smoothly again. When it comes to TIG welding pipe or anything else the key to good weld quality is cleanliness!